Chemical & Oil Compatibility Testing
Insulation systems need to continue to function when exposed to a range of chemicals – whether this exposure is unintended (e.g. from spillage) or intentional (e.g. in oil filled machines). Where materials are not compatible, the functional performance of an insulation system can be degraded over time. In higher voltage systems, this can then lead to complete electrical failure. We can expose insulation to a range of chemicals and carry out testing before / after exposure to confirm the impact that this has had on the insulation performance. Common fluids used in the laboratory include aerospace oils such as Mobil-Jet II and hydraulic fluids such as Skydrol.
Relevant Standards
Assessing the chemical compatibility of an insulation system within a laboratory can be guided by a range of standards with the two key ones being ASTM D543-21- Standard Practices for Evaluating the Resistance of Plastics to Chemical Reagents and ISO 175 - Plastics — Methods of test for the determination of the effects of immersion in liquid chemicals.
These standards describe a technique by which a plastic is immersed in a chemical for a period of 1 week (or in the case of the ISO standard up to 16 weeks). A concentration of test liquid of 8ml / square centimetre of sample is recommended by the ISO standard (with similar levels being defined in the ASTM standard). Tests at concentrations outside of this range are possible and in many cases it may be appropriate to use a ratio of volume / area according to that seen in the customer system.
Samples are then measured to assess the level of physical change. Within these standards the type of change usually examined relates to the sample mass / tensile strength etc. However, this can clearly be extended to include an analysis of electrical performance.
Samples are then measured to assess the level of physical change. Within these standards the type of change usually examined relates to the sample mass / tensile strength etc. However, this can clearly be extended to include an analysis of electrical performance.
Similarly, IEC 60216-1 describes how to conduct accelerated thermal ageing tests on insulating materials by subjecting the materials to constant, elevated temperatures. The standard outlines criteria and procedures for monitoring the degradation of key properties (such as electrical, mechanical, or chemical characteristics) as the material ages. This degradation is used as an indicator of the material's remaining useful life. Use can be made of this standard to guide ageing times when an insulation system is operated in contact with a chemical for extended periods.
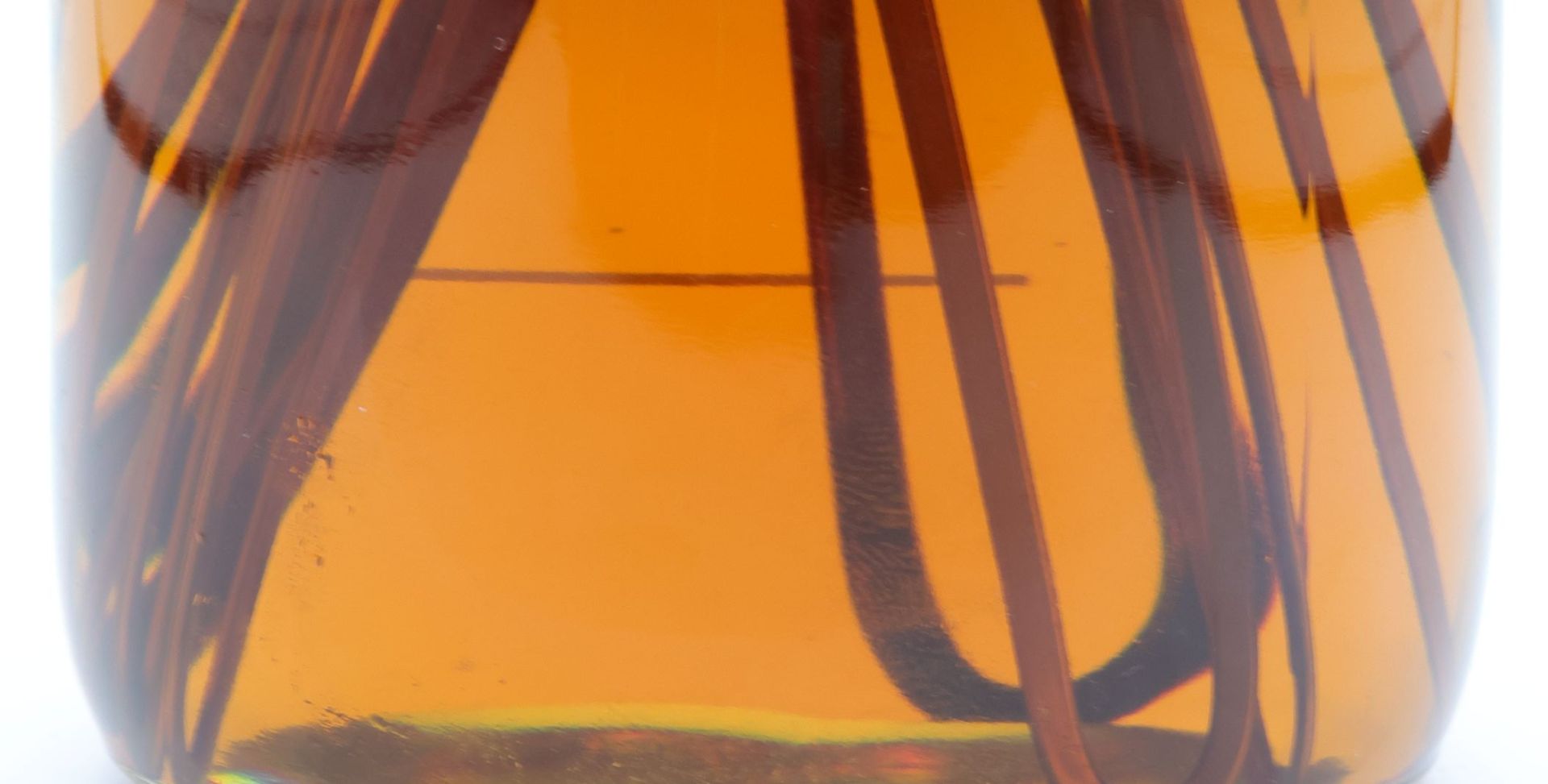
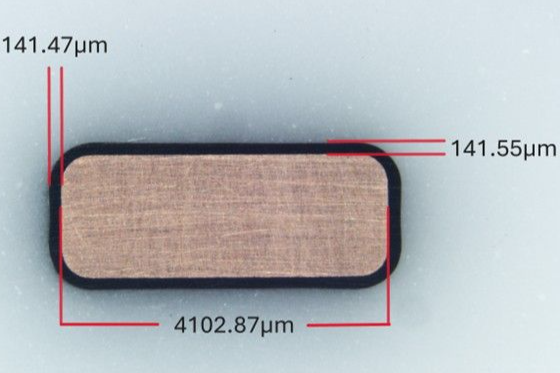
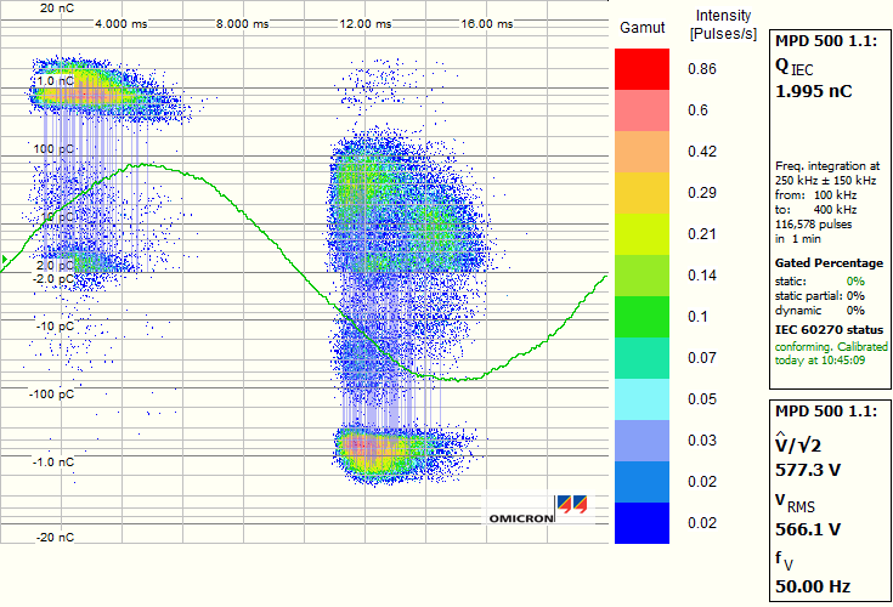
Typical Test Service
Carrying out a test to assess the compatibility of insulation with an oil or chemical typically involves the following steps
- Diagnostic Measurements Before Ageing: These will usually include insulation mass / thickness, electrical permittivity / loss angle, partial discharge inception voltage and breakdown voltage. Additionally, we can measure tensile strength / hardness depending on sample form.
- Ageing: Ageing can be carried out within an oven (so the insulation system and the fluid are all at the same temperature) or through the use of joule heating in conjunction with fluid flow in (this is useful when testing insulated wires where the wire temperature may be higher than the fluid temperature). Ageing periods can vary and may be chosen based on the operating cycle of the equipment.
- Diagnostic Measurements After Ageing: These measurements will be a repeat of those above. If multiple insulation materials are being assessed, the diagnostic measurements can be compared to identify the best performing material / system.
Contact
-
aHV Solutions
Manchester Science Park, Unit 3, Rutherford House, 40 Pencroft Way, Manchester M15 6SZ -
training@aerospacehv.com
-
+44 7410580864